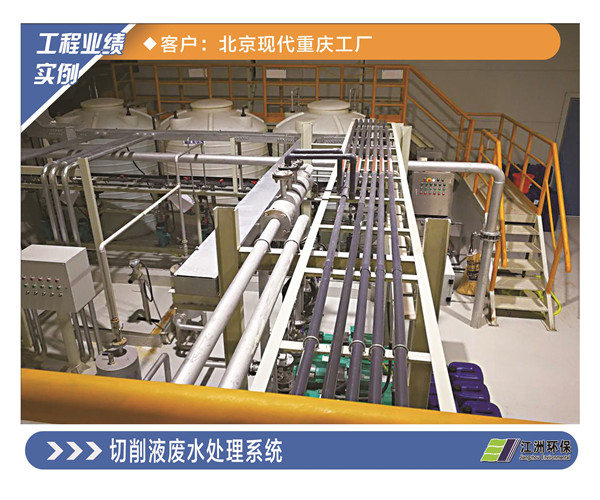
Name: Cutting fluid wastewater treatment system
Customer: Beijing Hyundai Chongqing Factory
Address: Chongqing Delivery time: October 2017
explain:
1. Wastewater inflow index:
Project concentration (mg/L) | COD | SS | Petroleum | nickel | PH |
|
Cutting fluid wastewater | ≤60000 | ≤600 | ≤20 | ≤0.1 | 5~9 |
2. Wastewater treatment discharge standard: pH, chemical oxygen demand, suspended solids and heavy metal discharge concentration of the main discharge outlet meet the Class II standard of Integrated Wastewater Discharge Standard (GB8978-1996). See the attached table for details:
S/N | Contaminants | emission standard |
one | PH | 6-9 |
two | COD(mg/L) | one hundred and fifty |
three | Suspended solids (mg/L) | one hundred and fifty |
four | Petroleum | ten |
five | Ammonia nitrogen | twenty-five |
6 | Chromaticity (dilution ratio) | eighty |
3. Process flow description
The waste cutting fluid discharged from the production workshop enters the waste cutting fluid collecting tank after intercepting the large particle suspended solids through the grid slot and settling the large particle iron chips in the grit chamber. The clear liquid separated through the iron chip separator enters the demulsification reaction tank. After full reaction, the oil-water separation is carried out through the waste oil separator. The separated waste oil is stored and outsourced for treatment; The separated clean water is sent to the primary treatment tank for treatment. After being chemically oxidized by strong oxidant, the treated clean water is subjected to coagulation reaction. The effluent after reaction is solid-liquid separated through the air flotation sedimentation tank. After being evenly mixed with domestic sewage in the mixing tank, the supernatant is sent to the secondary treatment tank for biochemical treatment. After being filtered, the supernatant is sent to the wastewater treatment plant up to standard. The sludge generated in the air flotation sedimentation tank is discharged into the sludge thickening tank, which is dewatered by the plate and frame filter press before being outsourced for treatment. The filtrate after pressure filtration flows back to the waste chip liquid sump for reprocessing.