According to the electrolytic law, only the average thickness of the whole surface of the plated part can be calculated. Practice has proved that even on the plane cathode with the same cathode distance, the distribution of current density and coating is uneven. The coating thickness on the sharp corners and edges is obviously greater than the average thickness, and the thickness on the central surface of the plane cathode is obviously less than the deviation of the average thickness by about 20-30%, This deviation can reach 500-700% on the surface of parts with complex shapes. Why is there such a deviation? The reasons are:
1. In electroplating, it is the flat part with the simplest shape in time. Because of the edge effect of current, the power line is easy to concentrate on the sharp corners and edges of the part, and the current density is relatively large, so the coating thickness is greater than the average thickness, while the power line is relatively small in the middle, and the current density is small, so the coating thickness is less than the average thickness.
2. For complex parts with uneven shapes or deep holes, in addition to the edge effect of current Electroplating equipment manufacturer Also, due to the uneven shape, the distance between the two anodes is different, so the ohmic point resistance between them is also different, Electroplating equipment As a result, the distribution of current density in uneven places is also different. The different places are close to the anode, the resistance is small, and the current density is large. The coating is thick. On the contrary, the coating wave that emerges even in the deep hole with smaller diameter will not deposit the coating because the power line cannot reach the inner wall surface.
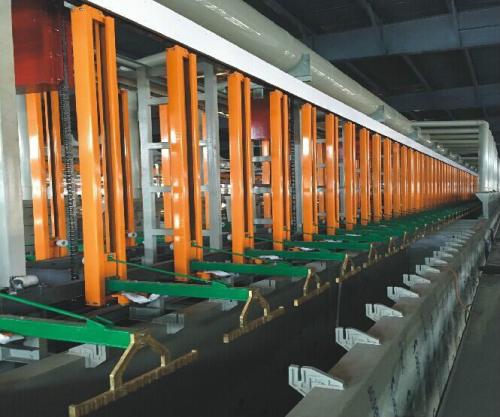
Each crane is composed of two hooks, namely hook A and hook B. Hook A is the workpiece to be plated, and hook B is used to exchange workpieces. The crane switches stations. Hook B first lifts the hollow hook in the slot, and then puts the pendant in hook A into the slot, so that it is easy to send the workpiece to the next crane and complete the following process flow. In the process flow of Crane 1, there is a link of chemical degreasing. Due to the long time of chemical degreasing, there is a switching function between tanks A and B. Crane 1 puts the workpiece into groove A for degreasing for the first time. After completing a cycle, the crane puts the workpiece into groove B for the second time, and then lifts the workpiece in groove A to enter the next process. This can save working time and improve work efficiency. The time of chemical degreasing, electrolytic degreasing, pre silver plating, silver plating, anti discoloration, activation, tin plating, neutralization, loading and unloading is adjusted by the touch screen at will.