Electroplating equipment The simple cleaning method in the past has been changed, and a new cleaning method - ultrasonic cleaning has been adopted. With ultrasonic cleaning, electroplating equipment can be cleaned quickly and efficiently. The cleaning temperature, concentration, time, etc. shall be determined through tests according to the oil residue of the plated parts, cleanliness requirements, cleaning methods, and drying methods, so that the ultrasonic cleaning can be more thorough. On the one hand, the ultrasonic cleaning method is mainly used to clean grease and greasy dirt of parts made of electroplated parts; At the same time, it is also applicable to the cleaning of residual grease and greasy dirt in the process of mechanical processing of parts and components made of electroplated parts in automobile, motorcycle, locomotive, refrigeration and air conditioning, compressor, diesel engine, numerical control equipment, communication equipment and other industries and their supporting enterprises.
Reducing energy consumption in the production process is a problem that many electroplating enterprises should pay attention to, Automatic electroplating line manufacturer As long as electroplating enterprises implement scientific management, comprehensively consider the selection of electroplating equipment and process, and strictly control the process and operation, they can completely achieve the purpose of saving energy and reducing electroplating costs. Therefore, we should better use electroplating equipment to achieve better energy-saving effects. The energy saving of Jiangsu electroplating equipment is reflected in the following aspects:
First, the concept of electroplating current efficiency has a very important meaning in production practice. Improving current efficiency can save electric energy. The current efficiency of various electroplating processes is quite different. If high-speed chrome plating process is adopted, the energy-saving effect is quite obvious, and the wind turbine power is saved, and the exhaust emission is reduced. Under the condition of meeting the technical requirements of the product, the high-efficiency electroplating process should be selected to save production costs.
Second, the selection of electroplating power supply is directly related to the coating quality, bath production capacity, energy consumption and investment benefits. Electroplating wastewater zero discharge manufacturer DC motor has been basically eliminated due to its high energy consumption and low efficiency; The price of silicon rectifier power supply is low, but the efficiency is not ideal. In order to further improve the efficiency of rectifier equipment, reduce the volume and weight of the whole machine, high-frequency switching power supply equipment has recently been produced. Although the price of switching power supply equipment is high, the investment can be recovered quickly and the electroplating quality can be improved.
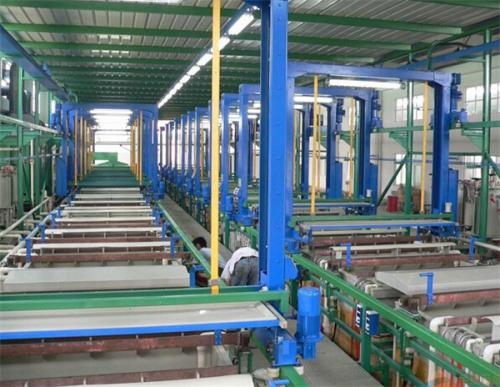
The electroplating solution must be used during the electroplating process. The waste solution after use contains a large amount of heavy metals. If it is directly discharged without good recovery and treatment equipment, it will cause serious pollution to the environment, and rivers, soil and groundwater cannot be spared; In addition, the staff are in the workshop where the electroplating equipment works for a long time, and as time passes, "electroplating occupational disease" will appear; The third is the harm to human health. Electroplating pollution will make people sick and affect human health.