Electroplating equipment It is necessary to finish the surface of parts to make them have a smooth and clean surface. This is an important link to obtain high-quality coating. So this link needs some auxiliary equipment to complete. What equipment are there?
1. The electroplating tank must be equipped with accessories including anode and anode basket or anode hook, electrode rod, power connection wire, etc. In order to save investment, some factories can hang the anode directly to the plating tank with a hook instead of an anode basket, but at least the anode sleeve should be put on.
2. Filtering and circulating filtering equipment. In order to ensure the electroplating quality, the plating solution needs to be filtered regularly. Some plating seeds are also required to be circularly filtered during operation. The filter is a common equipment in the chemical industry, so it is an industry standard equipment. However, it is also based on the enterprise's own standards. The filter is selected according to the plating type, tank size and process needs.
3. Heating or cooling device. Since the plating solution needs to work at a certain temperature, the plating tank should be equipped with heating equipment. For example, the bath temperature for bright nickel plating needs to be kept at 50 ℃, the temperature for chromium plating needs to be 50-60 ℃, and the temperature for acid bright copper plating or bright silver plating needs to be within 30 ℃. In this way, these process requirements need to be met by heat exchange equipment. Manufacturer of electroplating wastewater treatment equipment Generally, direct heating is used for heating.
4. Cathode moving or stirring device. Some plating seeds or most plating seeds need the cathode to be in the swing state, which can increase the working current, make the plating solution play its due role (usually brightness and dispersion ability), and prevent the tip, corner plating and scorching.
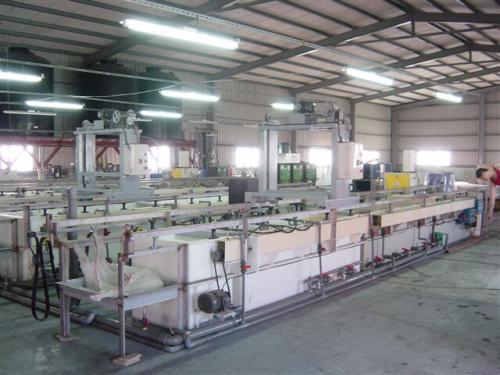
At present, electroplating equipment is a popular machine, but we may not have a comprehensive understanding of its electroplating technology, so today we follow Jiangsu electroplating equipment technicians to have a unified understanding of electroplating capabilities.
1. Leveling ability: Leveling ability (i.e. micro dispersion ability) refers to the ability of the plating solution of the electroplating equipment to make the micro profile of the coating smoother than the substrate surface when the coating is formed on the metal surface. It expresses the uniformity of coating distribution on the surface where the roughness of the base metal is relatively small, the depth of the wave cavity is less than 0.5mm, and the distance between the wave crest and the wave trough is very small.
2. Covering ability: covering ability (or deep plating ability) is also an important performance index of the plating solution, which refers to the ability to fully cover the deposited metal on the surface of cathode parts under certain electrolytic conditions, that is, the ability to deposit metal coatings in grooves or deep holes under specific conditions, which refers to the integrity of the distribution of coatings on parts.
Hydrogen embrittlement: after cathodic reduction of hydrogen ions, part of the hydrogen escapes, and part of the hydrogen penetrates into the base metal (especially high-strength metal materials) and coating in the form of atomic hydrogen, making the toughness of the base metal and coating decrease and become brittle. This phenomenon is called "hydrogen embrittlement".
3. Dispersion ability: The dispersion ability of the plating solution refers to the ability to make the deposited metal evenly distributed on the surface of cathode parts under certain electrolytic conditions.
Alloy plating: the process of co deposition of two or more metal ions on the cathode to form a uniform and fine coating is called alloy plating (generally, the minimum content should be greater than 1%).