With the rapid development of China, Electroplating equipment It has become an indispensable part of the production workshop. In order to complete electroplating processing according to process requirements in industrial production, not only power supply and electroplating tank, but also some auxiliary equipment are required to ensure the normal production of electroplating. It includes cathode moving or mixing equipment, heating or cooling equipment, electroplating solution circulating or filtering equipment and necessary accessories of electroplating tank, such as electrode rod, electrode wire, anode and anode basket, electroplating rack, etc. It can be seen that auxiliary equipment plays an important role in industry.
The main parameters affecting electroplating output are:
1、 Beat time requirements:
The beat time refers to the time required for the next hanging (or bucket) of workpiece. Generally speaking, the shorter the beat time, the more hanging (or barrels) produced per unit time.
For linear electroplating production lines, the beat time is generally ≥ 4.5 minutes, and the shortest can be 3 minutes; for annular electroplating production lines, the beat time is generally ≥ 1 minute, and the shortest can be 35 seconds.
2、 Weight requirements for each hanging or barrel of plated parts:
For hanging plating pieces, the quantity of each hanging plating piece is related to the size of the tank, and is generally measured by pieces or weight.
Discharge range of electroplated workpieces: the horizontal direction shall be 200mm smaller than the size of the tank, and the height shall be 350-400mm smaller than the tank.
For barrel plated parts, the amount of plated parts per barrel is related to the size of barrel, and is generally measured by weight. The discharge of electroplated workpieces generally does not exceed one-third of the total capacity of the barrel.
The output of the automatic electroplating production line is related to the beat time (minutes) and the plating quantity G (kg or pieces) per hang or barrel. Output per hour: KG × (60/T)
1. Cathode moving or agitator
In industrial processing, some seed electroplating is carried out on the vagina or in the state of stirring and swinging to increase the working current, which is the biggest role of the plating solution and can prevent the electroplating, burning and other functions of the needle tip and edge hairs.
2. Cooling or heating equipment
Since the bath needs to work at a certain temperature, it is necessary to install heating equipment on the bath. For example, bright nickel plating requires the bath temperature to be kept at 50 ℃, chromium plating temperature to be kept at 50-60 ℃, while acid bright copper plating or bright silver plating requires the temperature to be lower than 30 ℃. Direct heating is usually used for heating.
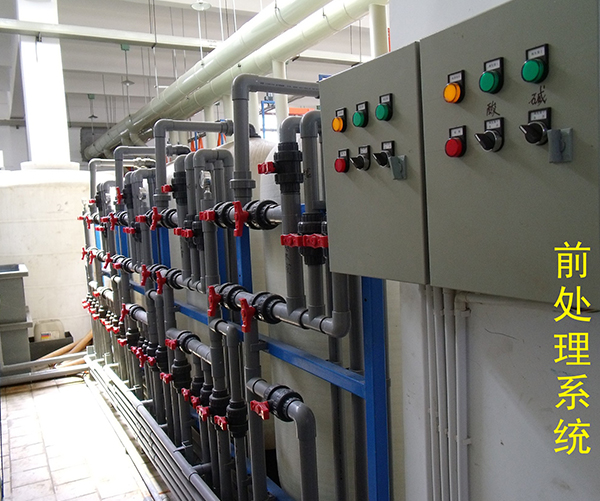
3. Filtering and circulating filtering
In order to ensure the electroplating quality, the plating solution needs to be filtered regularly. Some electroplating also requires continuous cycle filtration. Filters are commonly used equipment in the chemical industry, and electroplating equipment has industry standard equipment. Filter can be selected according to seed plating conditions, bath size and process requirements.
4. Necessary accessories for electroplating tank
The electroplating tank must be equipped with accessories, including anode and anode basket or anode hook, electrode rod, power connection wire, etc., and covered with anode sleeve. In order to save investment, some factories do not need anode baskets. The anode can also be directly hung in the electroplating tank with a hook.
The professional electroplating workshop can be an all-round automatic electroplating production line or a production mode of manual electroplating operation. The workshop completed the whole process from pre plating, electroplating to post plating. Under the leadership of the company or factory, qualified workshops can independently set up full-time departments (or personnel) such as production planning (scheduling), process management, quality inspection and direct cost management to fully complete product processing tasks. In the case of many varieties, few batches and unstable orders, a comprehensive processing electroplating workshop can be set up according to the general process requirements of electroplating to meet the requirements of market orders. In the electroplating workshop, the products can be divided into hanging plating and barrel plating, and the processes can be divided into zinc plating, copper plating, nickel plating, chromium plating, etc., to establish a section or section for production. In this section or group, the whole process of products from pre plating, electroplating and post-treatment can be completed in an all-round way, or pre plating can be carried out independently. A professional pretreatment section or group can be established. The products can be completed before and after electroplating and delivered to each electroplating factory. The electroplating section or group shall carry out subsequent processing until the product electroplating is completed in sequence.