Jiangsu Jiangzhou Environmental Protection Co., Ltd. has been committed to Electroplating equipment , Electroplating wastewater treatment equipment , Waste gas treatment equipment , an enterprise engaged in the research and development, design and manufacturing, sales and service of coating equipment. We can independently support copper, nickel and chromium plating line; Galvanizing barrel plating and hanging plating line; Circular line; ABS plastic and hydraulic hard chrome wire; Automatic electroplating lines for military and civilian products.
The company was founded in 2010 with a registered capital of 30 million yuan. The production process adopts numerical control processing, and the quality management system is strictly implemented in the production process, so that each project of "Jiangzhou" can reach the best standard, and the customer's demand is recognized by the customer. The company has passed ISO9002-1994 and ISO9001-2000 quality system certification, and is a member of China Surface Engineering Association, China Surface Plating Association and China Machinery Industry Federation.
For the surface condition and processing requirements during electroplating, select the appropriate steps to carry out necessary trimming and processing on the surface of the parts, so that the parts have a smooth and clean surface, which is an important link to obtain high-quality coating. In the pretreatment process of plating, the main equipment used are grinding, polishing machine, brushing machine, sandblasting machine, polishing machine and various fixed grooves. Electroplating is the main process in the whole production process. According to the requirements of parts, one or more single metal or alloy electroplating processes shall be selected for electroplating or immersion of parts to achieve the purpose of corrosion prevention, wear resistance and beauty. The equipment used in electroplating process mainly includes various fixed tanks, barrel plating tanks, hangers, baskets, etc. Post plating treatment refers to polishing, polishing, passivation, coloring, drying, sealing, dehydrogenation, etc. of parts, and one or more processes shall be selected as required to make the parts meet the quality requirements. The commonly used equipment for post plating treatment mainly includes grinding machine, polishing machine, various fixed grooves, etc.
Process requirements:
1. There should be good adhesion between the coating and the base metal, and between the coating and the coating.
2. The coating shall be crystal, smooth and even in thickness.
3. The coating shall have the specified thickness and as few pores as possible.
4. The coating shall have various specified indicators, such as brightness, hardness, conductivity, etc.
5. Plating time and temperature during electroplating determine the size of coating thickness.
6. The ambient temperature is - 10 ℃~60 ℃.
7. The input voltage is 220V ± 22V or 380V ± 38V.
8. The maximum working noise of water treatment equipment shall not be greater than 80dB (A).
9. The relative humidity (RH) shall not be greater than 95%.
10. The COD content of raw water is 100mg/L~150000mg/L.
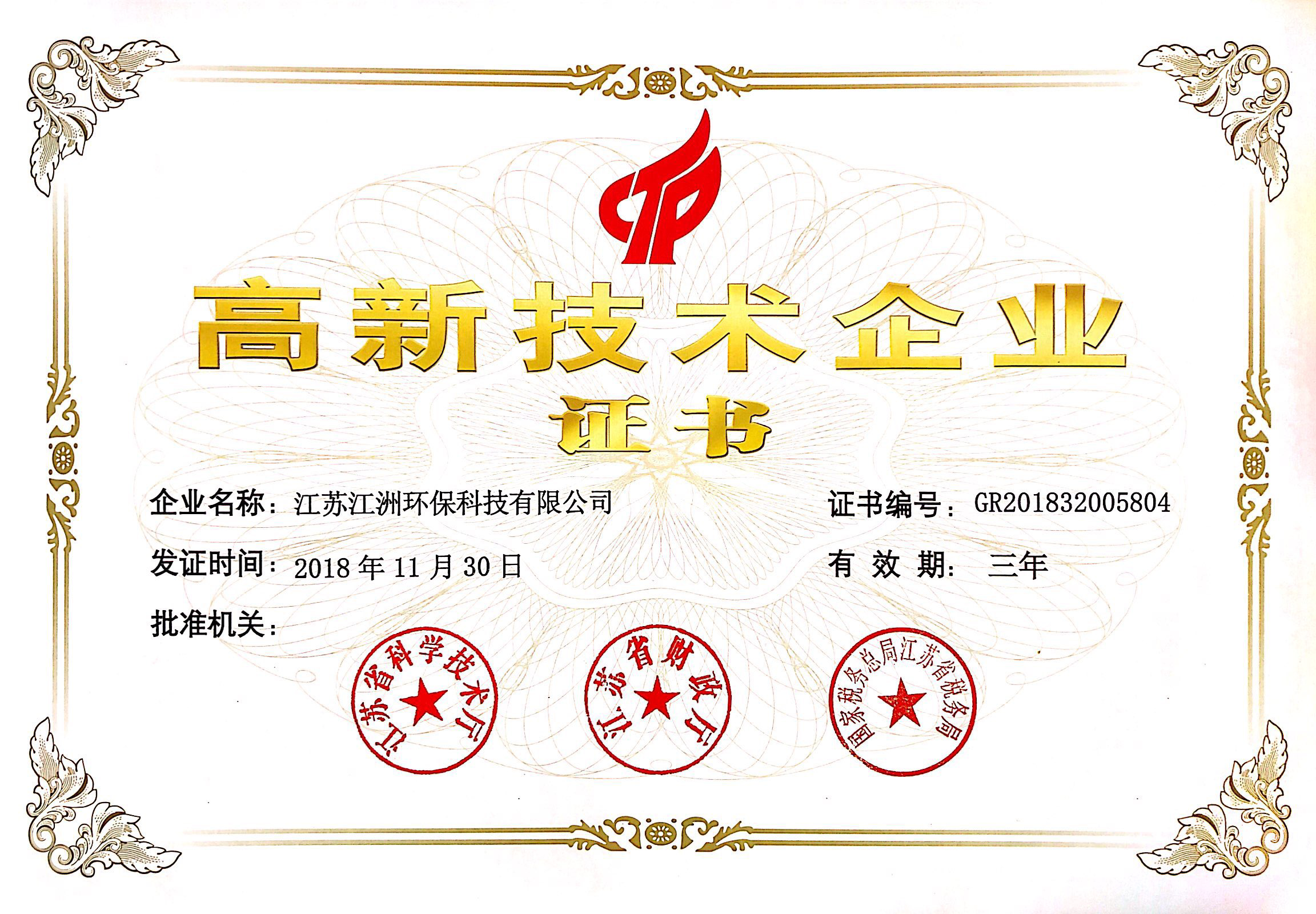
Through years of efforts, our company has gradually formed a multi-level, well-equipped technical support team. It can meet the all-round requirements of relevant projects in relevant fields. At the same time, the process has been constantly improved, and each link has formed a complete quality assurance system from design, manufacturing, installation, commissioning and after-sales service. Survival based on quality and development based on reputation are the source of continuous development of our company. Provide customers with timely, enthusiastic and considerate technical and after-sales services.
Electroplating technology:
Electroplating, also known as electrodeposition, is one of the main methods to obtain metal coatings on the surface of materials. It is the process of making the metal ions in the solution deposit on the surface of the cathode plated parts under the action of the DC electric field and forming a circuit by the anode and cathode in the electrolyte solution (plating solution); Current efficiency: the ratio of the electricity used to deposit metal to the total electricity is called current efficiency of electroplating.
Dispersion ability: The dispersion ability of the plating solution refers to the ability to make the deposited metal evenly distributed on the surface of cathode parts under certain electrolytic conditions.
Alloy plating: the process of co deposition of two or more metal ions on the cathode to form a uniform and fine coating is called alloy plating (generally, the minimum content should be greater than 1%).
Leveling ability: Leveling ability (i.e. micro dispersion ability) refers to the ability of the plating solution to make the micro profile of the coating smoother than the substrate surface when the coating is formed on the metal surface. It expresses the uniformity of coating distribution on the surface where the roughness of the base metal is relatively small, the depth of the wave cavity is less than 0.5mm, and the distance between the wave crest and the wave trough is very small.
Pinholes or pockmarks: hydrogen adheres to the cathode surface in the form of bubbles to prevent metal deposition at these parts. It can only be deposited around the bubbles. If hydrogen bubbles stay on the cathode surface throughout the electroplating process, the plated coating will have holes or through gaps; If hydrogen bubbles do not adhere firmly in the electroplating process, but escape and adhere intermittently and alternately, these parts will form shallow pits or pits, which are usually called pinholes or pockmarks in the electroplating industry.