What is the working principle of vertical continuous electroplating production line
The vertical continuous electroplating production line can shorten the raw material fiber or mixed particles by adding fine particles to form high-strength composite materials, improve the strength of plastic parts, master the rough pretreatment process of plastic electroplating parts, and achieve satisfactory results. It should be considered that the plastic is non-conductive and cannot be directly plated. It must be converted into a conductive cathode by depositing a conductive metal film.
Considering that improper shape will lead to local stress concentration of the workpiece and reduce the coating adhesion, it is required to avoid large areas of flat surface of electroplated plastic, round all edges and corners, not too thin, and not abrupt in thickness to ensure the coating quality. Plastic Electroplating equipment Higher requirements are put forward for the variety, shape and manufacturing process of plastics. At present, the main electroplating plastics are ABS, polypropylene and nylon, especially ABS plastics, which are most widely used and have the best electroplating effect.
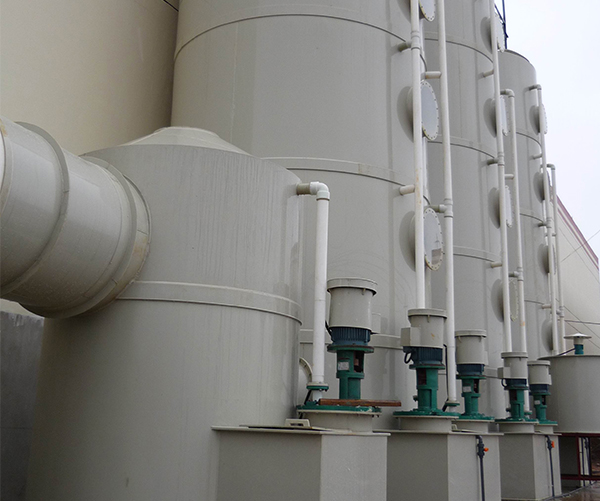
At present, an efficient and fast electroplating equipment can simultaneously plate multiple workpieces. Mixing the liquid medium in the electroplating process can accelerate the electroplating of the workpiece. Mixing the electroplating liquid medium filters impurities from the electroplating box, always adhere to the electroplating purity and quality, and greatly improve the electroplating efficiency, including the electroplating box, impurity filter, and agitator. The electroplating box is placed on the rack, and the electroplating box cover is placed on the upper end to contact and seal.
The upper end of the electroplating box cover is provided with several negative poles and electroplating workpieces. The lower end of the negative pole and electroplating workpieces extends into the electroplating box. The electroplating box is filled with electroplating liquid medium. The lower end of the negative pole and electroplating workpieces is immersed in liquid. The lower end of the electroplating box is provided with a row of mixers. The blades of the mixer are partially in the liquid medium, and the drive part is fixed on the rack. One end of the electroplating box is provided with a suction pipe, and the connection between the electroplating box and the suction pipe is provided with a one-way valve. The other end of the suction pipe is connected to the lower end of the impurity filter, the upper end of the impurity filter is connected to the extraction pump, the output end of the extraction pump is connected to the electroplating box through the discharge pipe, and the impurity filter and the extraction pump are placed on the pump support seat.