The control of process temperature is the top priority in the electroplating process. If the temperature fluctuates greatly, it will directly affect the quality of electroplating and cause energy waste. Existing Electroplating equipment This has been taken into account in the design, and the pre heating function is set on the human-computer interface, through which the pre heating time can be set. At the same time, the heating system of electroplating equipment is also equipped with liquid level control device, automatic water supplement device, etc., which can realize the function of automatic liquid level supplement of the system when the liquid level is lower than the set liquid level. So as to protect the system and prevent the heating pipe from dry burning or safety accidents. In addition, the use of PID fuzzy control is also to avoid adverse effects caused by temperature.
The traveling wheel of the crane adopts steel core and polyester rubber composite structure, and the imported magnetic induction proximity switch is used for parking positioning, Manufacturer of electroplating wastewater treatment equipment Imported frequency converter control and imported brand brake motor are used for operation, which ensures stable operation and accurate parking. Acid and alkali resistant pump, acid and alkali resistant vertical pump, self-priming pump operate continuously, with high production efficiency and large output. The fully automatic gantry type electroplating production line is automatically transported back to the flying target under computer control, which greatly reduces the labor intensity of workers. The design of the production line is reasonable, the structure is compact, the floor area is small, and the working environment can be greatly improved.
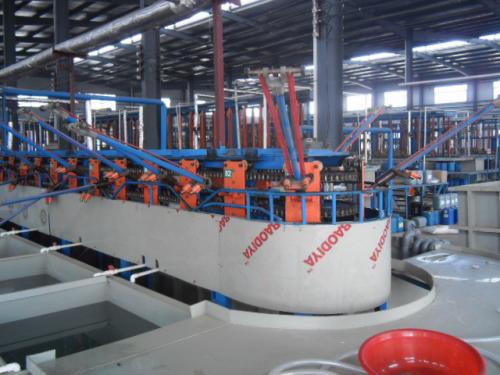
Not all metal ions can be deposited from the aqueous solution. If the side reaction of hydrogen ion reduction to hydrogen on the cathode is dominant, it is difficult for the electroplating equipment to precipitate metal ions on the cathode. According to the experiment, the possibility of metal ions electrodepositing from the aqueous solution can be obtained from the periodic table of elements. Anodes are divided into soluble anode and insoluble anode, Most anodes are soluble anodes corresponding to the coating, such as zinc anode for zinc plating, silver anode for silver plating, and tin lead alloy anode for tin plating. However, a few electroplating uses insoluble anodes due to the difficulty of anode dissolution, For example, platinum or titanium anodes are mostly used for acid gold plating. The main salt ions of the plating solution are supplemented by adding the prepared standard gold containing solution. Pure lead, lead tin alloy, lead antimony alloy and other insoluble anodes are used for chromium plating.
The main difference between the vertical plating line and the degree plating line is that the transport mode of the circuit board is different, while the maintenance and home care methods of the tank body are virtually the same. 7d Stop cleaning each water washing tank. For acid washing tank, stop cleaning once and change the tank liquid; Stop checking the spray installation in the tank to see if there is blockage, and stop dredging if there is blockage; For the conductive support on the copper plating bath and tin plating bath and the contact position between the anode and the front line, the wiping cloth and sandpaper can be used to stop polishing when the cleaning is stopped; Stop checking the titanium basket and tin bar basket of the copper plating bath and tin plating bath, replace the worn titanium basket bag and tin bar basket, and add copper balls and tin bars. After adding copper balls and tin bars in 7d, stop electrolysis of the copper plating bath and tin plating bath. 7d also needs to use high and low current modes to stop trial consumption, so that consumption can be stopped after the new copper balls and tin bars are added and the consumption performance is stable. Clean the copper ball and anode bag every 90. Stop filtering and cleaning the bath liquid with activated carbon every 120~150d, filter the impurities in the bath liquid, and stop cleaning the tin bath.