At present, most of the rectifier transformers are three-phase five column core energy-saving transformers, which eliminates the balance reactor than the six phase double inverted star rectifier with balance reactor, Electroplating equipment manufacturer It reduces costs and improves efficiency. The maintenance of thyristor power supply is more complicated. During the maintenance, the fault position shall be distinguished first. First, the DC voltage of the multimeter shall be 2.5V, the control pole shall be disconnected, and the voltage of the thyristor control pole shall be measured. Adjust the control knob. If the voltage is about 0~IV (different thyristors have different voltage values), the trigger control part is normal and the thyristors are faulty. If there is no voltage or the voltage value is very small, the trigger control board is faulty. First, check whether the working voltage and synchronous voltage input by the control board are normal. After the transformer fault of the working voltage and synchronous voltage provided is eliminated, the fault is concentrated on the trigger board, which needs to be replaced or sent for repair.
Electroplating equipment 9 precautions for polishing operation of the manufacturer
① Extract the wheel to be polished and check whether the wheel surface identification is consistent with its defects (pitting, pinhole, missing plating, insufficient brightness, inexhaustible wax removal, blistering, peeling, sanding, edge burning, poor displacement, bruise, sanding, roughness, deformation, etc.).
② According to the flow chart, the process is divided into processes, and the flow line operation (refers to copper billet) (see the flow line operation table).
③ When grinding, cloth drilling wheel or angle grinder polishing, the wheel should be placed stably. It is forbidden to press the power line on the wheel to prevent electric shock accidents
④ For grinding, select the sand piece with the specified specification first, stick it firmly, grasp the wheel with one hand, rotate the wheel with one hand, grasp the grinder with the other hand, and grind back and forth freely without excessive force until there is no coating appearance defect.
⑤ For the cloth drilling wheel, both hands are required to hold the air mill tightly, and the wax is evenly applied to make it slightly contact the working face. High speed polishing is required, and no heavy pressure is allowed; In addition, cloth wheel heads of different sizes and tapers shall be selected according to the shape and size of the polished part; The cloth drilling wheel is mainly at the angle between the spoke and the rim (other tools cannot polish or grind in place, which cannot reach the electroplating standard before nickel) and the upper part of the PCD hole (bolt hole).
⑥ When polishing the angle grinder, both hands should hold the angle grinder tightly, and wax should be evenly applied. After polishing, the polishing material should leave the wheel surface, and the wheel should be rotated to the part to be polished with one hand Manufacturer of electroplating wastewater treatment equipment Hold the angle grinder tightly with both hands to polish the parts to be polished. The polishing machine shall not be overloaded. It is not allowed to press the polishing abrasive vigorously for polishing. Instead, it is allowed to wax evenly, place the polishing abrasive lightly against the part to be polished, and move back and forth easily.
⑦ When polishing with the polishing machine, stand firmly, hold the wheel with both hands, and the side B of the wheel rests on one leg (the leg is bent and stepped on the specially prepared step). Use both hands and feet, so that the wheel can lean lightly on the high-speed polishing abrasive, concentrate and concentrate. When waxing, the wheels must leave the polishing abrasive.
⑧ During operation, whether the operator grasps the tool or holds the workpiece, the tool or workpiece must be able to move back and forth freely. The workpiece must be in light contact with polishing or abrasive materials, otherwise it is easy to cause polishing or scrapping. Wax should be evenly applied when polishing the cloth wheel, and polishing wax should be scraped with a cloth wheel when polishing the final process, When polishing or grinding passes through the pre coating of the coating, stop polishing or grinding.
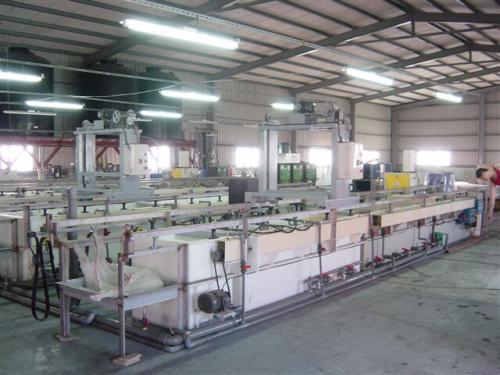
The main difference between the vertical plating line and the degree plating line is that the transport mode of the circuit board is different, while the maintenance and home care methods of the tank body are virtually the same. 7d Stop cleaning each water washing tank. For acid washing tank, stop cleaning once and change the tank liquid; Stop checking the spray installation in the tank to see if there is blockage, and stop dredging if there is blockage; For the conductive support on the copper plating bath and tin plating bath and the contact position between the anode and the front line, the wiping cloth and sandpaper can be used to stop polishing when the cleaning is stopped; Stop checking the titanium basket and tin bar basket of the copper plating bath and tin plating bath, replace the worn titanium basket bag and tin bar basket, and add copper balls and tin bars. After adding copper balls and tin bars in 7d, stop electrolysis of the copper plating bath and tin plating bath. 7d also needs to use high and low current modes to stop trial consumption, so that consumption can be stopped after the new copper balls and tin bars are added and the consumption performance is stable. Clean the copper ball and anode bag every 90. The electroplating equipment shall use activated carbon to filter and clean the bath solution every 120~150d, filter the impurities in the bath solution and clean the tin bath.