For the surface condition and processing requirements during electroplating, select the appropriate steps to carry out necessary trimming and processing on the surface of the parts, so that the parts have a smooth and clean surface, which is an important link to obtain high-quality coating. In the pretreatment process of plating, the main equipment used are grinding, polishing machine, brushing machine, sandblasting machine, polishing machine and various fixed grooves. Electroplating is the main process in the whole production process. According to the requirements of parts, one or more single metal or alloy electroplating processes shall be selected for electroplating or immersion of parts to achieve the purpose of corrosion prevention, wear resistance and beauty. The equipment used in electroplating process mainly includes various fixed tanks, barrel plating tanks, hangers, baskets, etc. Post plating treatment refers to polishing, polishing, passivation, coloring, drying, sealing, dehydrogenation, etc. of parts, and one or more processes shall be selected as required to make the parts meet the quality requirements. The commonly used equipment for post plating treatment mainly includes grinding machine, polishing machine, various fixed grooves, etc.
Electroplating equipment And ultrasonic cleaning equipment. Electroplating is an electrochemical process, Electroplating wastewater zero discharge manufacturer It is also an oxidation-reduction process. The basic process of electroplating is to immerse the parts in the solution of metal salt as the cathode, and the metal plate as the anode. After the DC power supply is connected, the required coating is deposited on the parts.
For example, during nickel plating, the cathode is the part to be plated and the anode is a pure nickel plate. The following reactions occur at the cathode and anode respectively:
Cathode (plating piece): Ni2++2e → Ni (main reaction)
2H++2e → H2 ↑ (side reaction)
Anode (nickel plate): Ni-2e → Ni2+(main reaction)
4OH - - 4e → 2H2O+O2+4e (side reaction)
Process requirements:
1. There should be good adhesion between the coating and the base metal, and between the coating and the coating.
2. The coating shall be crystal, smooth and even in thickness.
3. The coating shall have the specified thickness and as few pores as possible.
4. The coating shall have specified indicators, such as brightness, hardness, conductivity, etc.
5. Plating time and temperature of electroplating process determine the size of coating thickness.
6. The ambient temperature is - 10 ℃~60 ℃.
7. The input voltage is 220V ± 22V or 380V ± 38V.
8. The maximum working noise of water treatment equipment shall not be greater than 80dB (A).
9. The relative humidity (RH) shall not be greater than 95%.
10. The COD content of raw water is 100mg/L~150000mg/L.
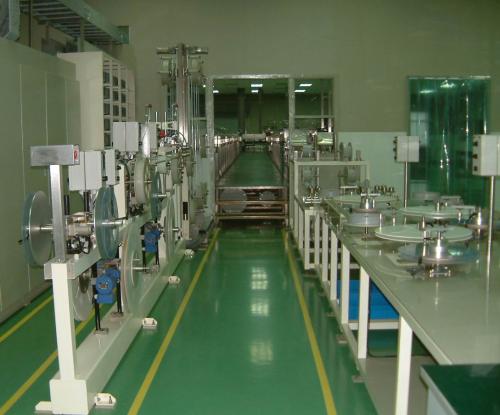
Electroplating, also known as electrodeposition, is one of the main methods to obtain metal coatings on the surface of materials. It refers to the process of making the metal ions in the solution deposit on the surface of cathode plated parts under the action of DC electric field, and the circuit of electroplating equipment is formed by anode and cathode in the electrolyte solution (plating solution); Current efficiency: the ratio of the electricity used to deposit metal to the total electricity is called current efficiency of electroplating.
Dispersion ability: The dispersion ability of the plating solution refers to the ability to make the deposited metal evenly distributed on the surface of cathode parts under certain electrolytic conditions.
Alloy plating: the process of co deposition of two or more metal ions on the cathode to form a uniform and fine coating is called alloy plating (generally, the minimum content should be greater than 1%).
Leveling ability: Leveling ability (i.e. micro dispersion ability) refers to the ability of the plating solution to make the micro profile of the coating smoother than the substrate surface when the coating is formed on the metal surface. It expresses the uniformity of coating distribution on the surface where the roughness of the base metal is relatively small, the depth of the wave cavity is less than 0.5mm, and the distance between the wave crest and the wave trough is very small.
Pinholes or pockmarks: hydrogen adheres to the cathode surface in the form of bubbles to prevent metal deposition at these parts. It can only be deposited around the bubbles. If hydrogen bubbles stay on the cathode surface throughout the electroplating process, the plated coating will have holes or through gaps; If hydrogen bubbles do not adhere firmly in the electroplating process, but escape and adhere intermittently and alternately, these parts will form shallow pits or pits, which are usually called pinholes or pockmarks in the electroplating industry.
Bubbling: after electroplating, when the temperature of the surrounding medium rises, the adsorbed hydrogen accumulated in the base metal will expand, resulting in small bubbles in the coating, which seriously affects the quality of the coating. This phenomenon is especially obvious in electrogalvanizing, cadmium, lead and other metals.