1. The last method of brush plating is called "brush plating": it is an electrodeposition technology, and not all parts are immersed in the electrolyte during the electroplating process. In this electroplating technology, only a limited area is electroplated, and there is no impact on the rest..
2. Fingering Electroplating equipment In electroplating, rare metals are often required to be plated on board edge connectors, board edge protruding contacts or gold fingers to provide lower contact resistance and higher wear resistance. This technology is called finger plating or protruding part plating. In electroplating, gold is also often plated on the protruding contact of the board edge connector whose inner layer is nickel. The protruding part of the gold finger or the board edge is manually or automatically plated. At present, the gold plating on the contact plug or gold finger has been replaced by lead plating and button plating.
3. The pins and pins of roller linked selective plating electronic components, such as connectors, integrated circuits, transistors and flexible printed circuits, are all selectively plated to obtain good contact resistance and corrosion resistance. This electroplating method can adopt manual electroplating production line or automatic electroplating equipment, and it is very expensive to select and plate each contact pin separately, Electroplating wastewater treatment equipment Electroplating equipment manufacturer Therefore, it is necessary to use batch welding. In electroplating production, the two ends of the rolled metal foil with the required thickness are usually punched, cleaned by chemical or mechanical methods, and then selected to use nickel, gold, silver, rhodium, button or tin nickel alloy, copper nickel alloy, nickel lead alloy, etc. for continuous electroplating.
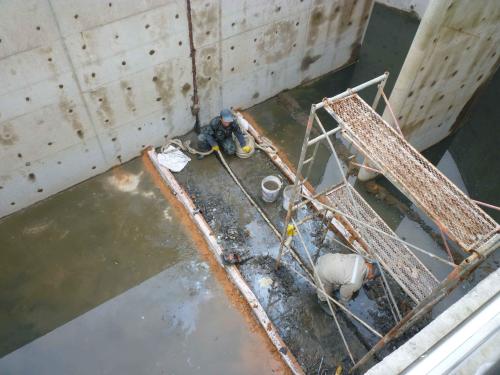
The maximum current can also be calculated according to the plating area. Taking chromium plating as an example, if the plating solution is 600L, the maximum current density allowed by the plating equipment is 100A/dm2 at 60 ℃, and if the plating tank can be plated with 10dm2 when it is fully loaded, the maximum output current of the required power supply is 100A/dm2 × 10dm2=1000A, that is, 1000A, 18V rectifier power supply shall be configured. After determining the power of the power supply. The waveform, cooling mode, volume and corrosion resistance of the electroplating power supply should also be selected according to the needs of the electroplating process and the conditions of the electroplating site, including cost factors.
Therefore, the selection of electroplating equipment power supply equipment also has knowledge, which needs to meet three requirements: meet the specifications required by the electroplating process, the power size of the power supply, waveform indicators, and the adjustable range of the current voltage value; The reliability of the power supply itself, which mainly refers to the rationality and safety of the structure, as well as the characteristics of the circuit, cooling mode, etc; The price performance ratio should be considered.