Not all metal ions can precipitate from aqueous solution. If the side reaction of hydrogen ion reduction to hydrogen is dominant on the cathode, it is difficult for metal ions to precipitate on the cathode. According to the experimental results, the possibility of electrodeposition of metal ions in aqueous solution can be obtained from the periodic table of elements. Anodes can be divided into soluble anodes and insoluble anodes, most of which are soluble anodes and insoluble anodes. Soluble anode corresponding to the coating, such as zinc anode, silver anode, tin lead alloy anode, but because of the difficulty of anode dissolution, insoluble anode used in electroplating, such as acid gold plating, is mostly platinum or titanium anode, and the main salt ions of electroplating solution are supplemented. By adding standard gold containing solution, pure lead is used as chromium plating anode. Lead tin alloy, lead antimony alloy and other insoluble anodes.
Generally speaking, rolling polishing (commonly known as rolling polishing) is to put small machines and abrasives as well as rolling liquid into the float or bell drum, because the rotation of the float makes the whole machine and the whole machine, the whole machine and abrasives conflict with each other, plus the chemical action of rolling polishing liquid, and in addition to blood stains and rust products in the name, The whole machine has also corrected the non-metallic names, thus losing the smoothness and luster of the names. All auxiliary facilities are designed to make parts lose better coating after silver plating. Rolling light is the process of putting the whole machine into the buoy containing abrasive and chemical filtrate, so that the whole machine and abrasive, the whole machine and the whole machine collide with each other through the buoy to reach the name of the clearing machine. Let's look at the rolling light. Centrifugal disc polishing is characterized by fast polishing speed, and the polishing quality is equivalent to that of centrifugal roller polishing.
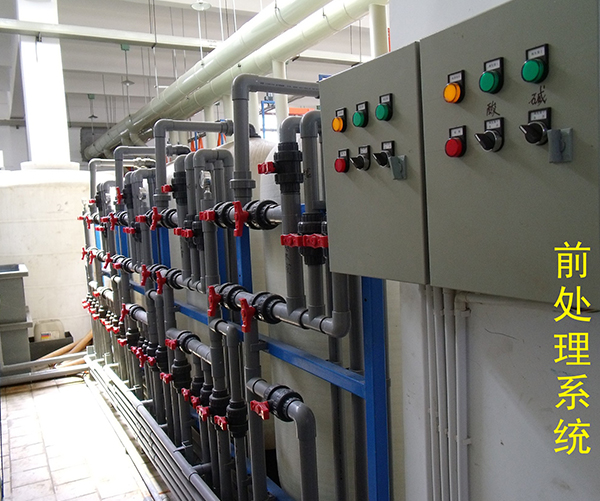
Electroplating equipment Analysis of system temperature control:
1。 The production efficiency of equipment will be greatly improved by setting the preheating function and time on the man-machine interface to realize the management of the preheating system for high-temperature process.
2。 The heating system is equipped with a liquid level control device and an automatic water supplement device. When the liquid level is lower than the set level, the system will automatically supplement, and the electroplating equipment will reasonably protect the system to prevent the heating pipe from dry burning. At the same time, each electric heating system has reliable grounding protection measures to avoid safety accidents.
3。 In electroplating process, process temperature control is very important. If the temperature fluctuation is too large, it will not only cause waste of electric energy, but also have a great impact on product quality. PID fuzzy control can effectively reduce or even avoid these problems.
The main difference between vertical plating line and degree plating line is that the transport mode of circuit board is different, while the maintenance method of battery body is basically the same. Stop cleaning the pickling tank once every 7 days, stop cleaning once, and replace the bath solution; Stop checking the sprinkler in the water tank, check whether there is blockage, and stop the blockage in time; Stop the contact position between the conductive support on the copper plating bath, tin plating bath and flange and the anode. T line; Stop cleaning once, and stop polishing with cloth and sandpaper; The titanium basket and tin bar basket of copper plating bath and tin plating bath shall be checked once and replaced with titanium basket and tin bar basket. Copper ball and tin bar shall be added. Stop electrolytic copper plating bath and tin bath after adding copper ball and tin bar within 7 days. In 7 days, it is also necessary to stop the consumption test in the high and low current modes, so that after adding new copper balls and tin rods, the consumption performance will be stable before stopping consumption. Stop cleaning the copper ball and anode bag every 90 minutes. Every 120 to 150 days, stop filtering and cleaning the tin bath with activated carbon, remove impurities in the tin bath, and stop cleaning the tin bath once.