There are three requirements for the selection of electroplating power supply equipment: first, meet the specifications required by the electroplating process, including the power size of the power supply, waveform indicators, and the adjustable range of current and voltage values; The second is the reliability of the power supply itself, which mainly refers to the rationality and safety of the structure, as well as the characteristics of the circuit, cooling mode, etc; Third, consider the price performance ratio
To determine how large and what kind of power supply should be configured for a plating type and all plating tanks is the first important work for electroplating production. In actual production Electroplating equipment manufacturer There are two methods to determine the electroplating power supply: one is the volume current density method to be determined according to the bath capacity; The other is the unit area current density method calculated according to the plating area.
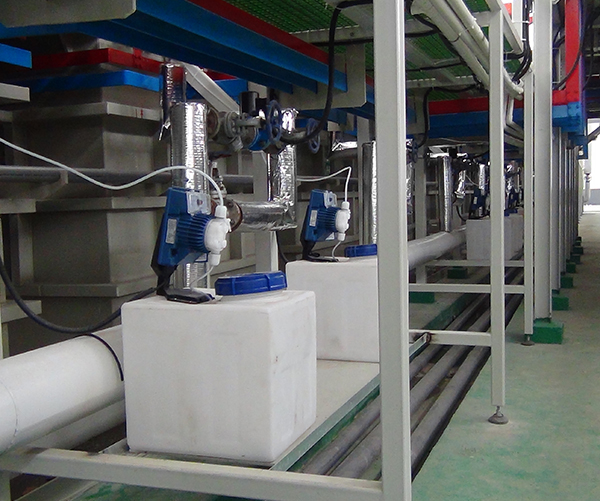
The so-called volume current density is to adjust the current intensity that the entire plating bath needs to pass according to the maximum current allowed for each liter of plating solution, so as to determine the maximum power supply to be used and the power of conventional output. Copper plating is generally 0.2~0.3A/L, nickel plating is 0.1~2.5A/L, bright nickel plating is 0.3~0.35A/L, acid zinc plating is 0.5~0.6A/L, alkaline zinc plating can reach 1.2A/L, and chromium plating is 2~3A/L. Taking bright nickel plating as an example, the maximum process current of 600L plating solution can reach 0.3A/L × 600L=180A, so 200A power supply is enough.
The maximum current can also be calculated according to the plating area. Taking chromium plating as an example, if it is a 600L plating solution, the maximum allowable current density is 100A/dm2 at 60 ℃. If the plating tank can be plated with 10dm2 when it is fully loaded, the maximum output current of the required power supply is 100A/dm2 × 10dm2=1000A, that is, 1000A, 18V rectifier power supply shall be configured.
After determining the power of the power supply. The waveform, cooling mode, volume and corrosion resistance of the electroplating power supply should also be selected according to the needs of the electroplating process and the conditions of the electroplating site, including cost factors.