Electroplating equipment How additives function and mechanism
Electroplating is a scientific process widely used in agriculture, industry, science and technology, transportation, electronics and other industries as well as in daily necessities. The production of electroplating not only makes metal less corrosive and plastic products more durable, but also makes the appearance of these products more beautiful. It is also because of these excellent properties of electroplating products that, Electroplating products are almost everywhere.
In people's opinion, a good electroplating product should have a smooth and moist appearance, a uniform and delicate surface, and not fade, rust, or peel off when used. In order to improve the performance and beauty of electroplating products, it is often necessary to add some additives to improve the smoothness and gloss of products during electroplating.
For example, blue zinc passivation solution, color zinc passivation solution, black passivation solution, etc. are often used in galvanized products. As the name suggests, the role of galvanized passivation solution is to make the product not easy to interact with oxygen in the air and prevent oxidation. The addition of blue zinc passivation solution increases the blue brightness of the electroplated parts, and also makes the brightness of the electroplated products more uniform and improves the product grade. Of course, it also plays a role in increasing the firmness and corrosion resistance of the electroplated film, and also increases the anti collision ability of the products. Color zinc passivation solution will increase the glossiness of the galvanized layer, and the product will increase the corrosion resistance. It is not easy to scratch and decolour, and it will also feel more beautiful in the color of galvanized parts. Black passivation solution is to form a black protective film on the product surface, which makes the product look more noble and elegant.
Of course, these electroplating additives also have high requirements for operation. The temperature, concentration and PH of the solution will affect the electroplating effect. Frequent adjustment and strict compliance with operating procedures are required in the operation process.
Electroplating equipment manufacturer Additives include organic additives (such as coumarin for nickel plating) and inorganic additives (such as cadmium salt for copper plating). Most of the electroplating additives used in the early days were inorganic salts, and then organic substances gradually gained a leading position in the ranks of electroplating additives. According to function, electroplating additives can be divided into leveling agent, brightener, wetting agent and stress relieving agent. Additives with different functions generally have different structural characteristics and action mechanisms, but multifunctional additives are also common. For example, saccharin can be used as both a nickel plating brightener and a commonly used stress reliever; And additives with different functions may also follow the same action mechanism.
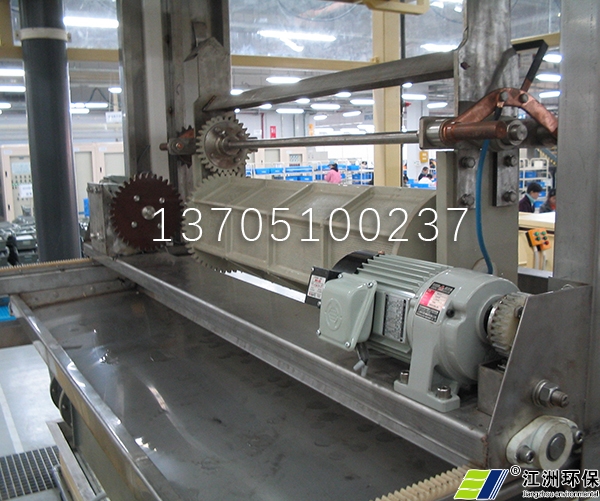
Action mechanism of electroplating additives
The electrodeposition process of metals is carried out step by step: first, the electroactive material particles migrate to the outer Helmholtz layer near the cathode for electro adsorption, then, the cathode charge is transferred to the partially desolvated ions or simple ions adsorbed on the electrode to form adsorbed atoms, and finally, the adsorbed atoms migrate on the electrode surface until incorporated into the lattice. The first process above all generates certain overpotential (migration overpotential
Activation overpotential and electrocrystallization overpotential). Only under a certain overvoltage, the electrodeposition process of metal can have a sufficiently high grain nucleation rate, medium charge transfer rate and a sufficiently high crystallization overvoltage, so as to ensure that the coating is smooth, compact, shiny and firmly bonded to the base material. Appropriate electroplating additives can improve the overpotential of metal electrodeposition and provide a strong guarantee for the quality of the coating.
1. Diffusion control mechanism
In most cases, the diffusion of additives to the cathode (rather than the diffusion of metal ions) determines the electrodeposition rate of metals. This is because the concentration of metal ions is generally 100~105 times that of additives. For metal ions, the current density of electrode reaction is far lower than its limit current density.
Under the control of additive diffusion, most of the additive particles diffuse and adsorb on the bulges, active parts and special crystal planes with high surface tension of the electrode, causing the adsorbed atoms on the electrode surface to migrate to the depression on the electrode surface and enter the lattice, thus playing a role in leveling and brightening.
2. Non proliferation control mechanism
According to the dominant non diffusion factors in electroplating, the non diffusion control mechanism of additives can be divided into electro adsorption mechanism, complex formation mechanism (including ion bridge mechanism), ion pair mechanism, mechanism of changing Helmholtz potential, mechanism of changing electrode surface tension, etc.