Electroplating equipment What is the basic principle?
Electroplating equipment is an electrochemical process as well as an oxidation-reduction process. The basic process of electroplating is to dip the parts in the solution of metal salt as the cathode, and the metal plate as the anode. After the DC power supply is connected, the required coating is deposited on the parts.
For example, during nickel plating, the cathode is the part to be plated and the anode is a pure nickel plate. The following reactions occur at the cathode and anode respectively:
Cathode (plated part): Ni 2+ +2e → Ni (main reaction)
2H + +e→H two ↑ (side reaction)
Anode (nickel plate): Ni-2e → Ni 2+ (Main reaction)
4OH - ﹣4e→2H two O+O two +4e (side reaction)
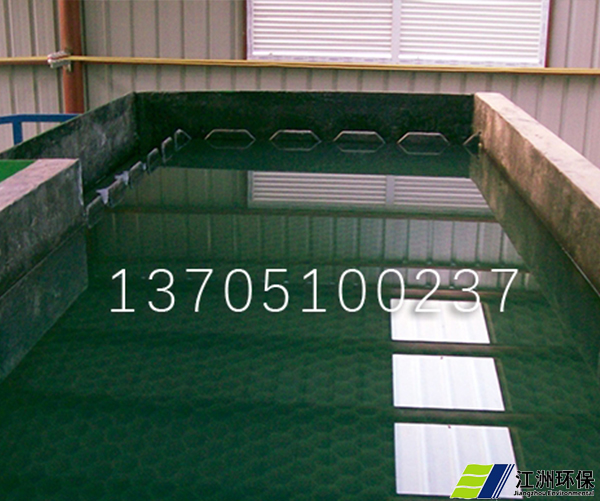
Not all metal ions can be deposited from aqueous solution. If the side reaction of hydrogen ion reduction to hydrogen on the cathode is dominant, it is difficult for metal ions to precipitate on the cathode. According to the experiment, the possibility of electrodeposition of metal ions from aqueous solution can be obtained from the periodic table of elements, as shown in Table 1.1
Anodes are divided into soluble anodes and insoluble anodes. Most anodes are soluble anodes corresponding to the coating, such as zinc anode for zinc plating, silver anode for silver plating, and tin lead alloy anode for tin lead alloy plating. However, a few electroplating uses insoluble anode due to the difficulty of anode dissolution. For example, platinum or titanium anode is mostly used for acid gold plating. The main salt ions of the plating solution are supplemented by adding the prepared standard gold containing solution. Chromium plating anode uses insoluble anode such as pure lead, lead tin alloy and lead antimony alloy.