Electroplating equipment What are the particularity of materials? The particularity of electroplating equipment material is porous. The Nd-Fe-B material made by powder pressing and sintering has porous surface, which has been machined before surface treatment. The pores on the surface of the material absorb many impurities (such as grease) that are harmful to the surface treatment or the coating of the magnet, and various high plating levels. Before the surface treatment, these harmful impurities drive out of the matrix, which is one of the key factors to ensure the good adhesion of the coating of the magnet. Hydrogen absorption behavior Nd-Fe-B magnet is a kind of hydrogen absorption material, which removes a small amount of oxygen adsorbed in the material before surface treatment.
1. Finger plating equipment often needs to plate rare metals on board edge connectors, board edge protruding contacts or gold fingers to provide lower contact resistance and higher wear resistance in electroplating. This technology is called finger plating or protruding part electroplating. In electroplating, gold is also often plated on the protruding contact of the board edge connector whose inner layer is nickel. The protruding part of the gold finger or the board edge is manually or automatically plated. At present, the gold plating on the contact plug or gold finger has been replaced by lead plating and button plating.
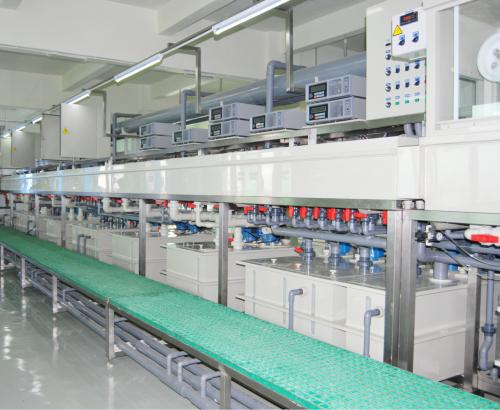
2. Through hole plating In through hole plating, there are many methods to establish a satisfactory plating layer on the hole wall drilled on the substrate, which is called hole wall activation in industrial applications. The commercial production process of its printed circuit requires multiple intermediate storage tanks. Each storage tank has its own control and maintenance requirements. Through hole electroplating is a necessary subsequent production process in the drilling process. When the drill bit drills through the copper foil and the substrate below, the heat generated will melt the insulating synthetic resin that forms the substrate of most substrates, and the molten resin and other drilling debris will accumulate around the holes, Apply to the newly exposed hole wall in the copper foil. Ink is used to form a high adhesion and high conductivity film on the inner wall of each through hole, so it is unnecessary to use multiple chemical treatment processes, Electroplating equipment manufacturer With only one application step and subsequent heat curing, a continuous coating can be formed on the inner side of all hole walls. It can be directly plated without further treatment. This kind of ink is a resin based material, which has a strong adhesion and can be easily bonded to most of the thermally polished hole walls, thus eliminating the step of back etching.
The particularity of electroplating equipment and materials is to minimize the occurrence of hydrogen absorption reaction of materials in the electroplating equipment factory during the plating process and to drive away the residual hydrogen in the materials and coating after plating, which is the key to ensure that the coating is not bulging. Abnormal thermal expansion and cold contraction Due to the existence of the expansion and contraction of the magnet, Nd-Fe-B materials are very temperature sensitive, Its linear expansion coefficient in the direction parallel to the orientation is (The linear expansion coefficient that is straight to the orientation direction, however, requires that the temperature and water adjustment be taken into account when selecting the coating and process. When the temperature changes, the tensile stress or compressive stress between the processes of the substrate and the coating will occur due to different linear expansion coefficients, so as to ensure that the coating will not appear cracking, peeling, and shadow. During the etching process of boron ash, the magnet surface will be attached with a layer of black gray powder, which It is the boron rich phase that the magnet dissolves and falls off that attaches to the surface of the magnet. This kind of boron ash is very difficult to wash off. It covers the surface of the material to make the coating and the substrate (the more effective method is to use ultrasonic cleaning to remove it.