The advantages of using membrane separation technology to treat electroplating rinse wastewater mainly include the following aspects:
1. Reuse of wastewater and reduce the amount of rinsing water can further treat the wastewater to meet the requirements of "zero discharge", reduce the scale of biochemical and physicochemical treatment, and help enterprises expand production;
2. It can recover useful metal ions, so that enterprises can achieve environmental protection goals and generate benefits at the same time;
3. The effluent quality of the membrane is good and transparent, which is higher than the process water requirements of the electroplating industry;
4. It can be designed according to the treatment requirements, and can continuously expand and increase the treatment capacity and improve the treatment performance through continuous optimization;
5. The system is easy to operate, highly automated, and occupies a small area;
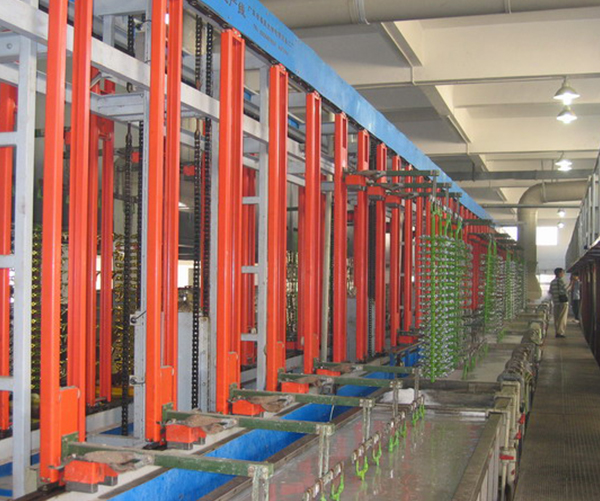
Treatment of Class III wastewater:
(a) Treatment of pickling wastewater:
Adjust the pH value of pickling wastewater to 6~9 with sodium hydroxide solution, aerate it with air for 2~12 hours, remove the precipitation, Zero discharge of electroplating wastewater The clarified solution removes metal cations through adsorption of hydrogen type strong acid cation exchange resin, and then concentrates and recovers low salt water through reverse osmosis device; The regeneration liquid of hydrogen type strong acid cation exchange resin is transported to the acid dissolving tank; After being concentrated by the reverse osmosis device, the high salt water is evaporated and concentrated to the solid after chelating resin and activated carbon adsorption, pH adjustment and flocculation treatment, and becomes harmless solid impurities. The condensed water is recycled for use, or the high salt water is treated by chelating ion exchange resin, and then discharged directly after the wastewater COD reaches the standard through ultraviolet photocatalytic oxidation;
(b) Treatment of cyanide containing wastewater:
The pH value of cyanide containing wastewater is controlled at 7~10. The cyanide ion in the wastewater is removed by the anion exchange resin treated by complexation anion, and then the copper and zinc ions in the wastewater are removed by the cation exchange resin adsorption. The wastewater enters the reverse osmosis system, and the low salt water is reused. The high salt water is removed by the chelating ion exchange resin, and the heavy metal ions are removed by the pH adjustment After flocculation treatment, it evaporates and concentrates to the solid to become harmless solid impurities. Condensate water is recycled for use, or high salt water is treated by chelating ion exchange resin and discharged directly after the COD reaches the standard through ultraviolet photocatalytic oxidation;
The anion exchange resin treated with complex anion is saturated after adsorption and regenerated with 4~6mol/L hydrochloric acid. The regenerated solution is recycled after removing hydrogen cyanide;
(c) Treatment of mixed wastewater from passivation and electroplating rinsing:
Control the pH value of the mixed wastewater of passivation and electroplating rinsing at 0~5, and remove hexavalent chromium ion through anion exchange resin adsorption; Adjust the pH value of wastewater to 5~10 to form sediment, and the sediment will be sent to the acid dissolving tank after pressure filtration and cleaning; The clarified solution is adsorbed and removed by the anion exchange resin with complex anion treatment, and then the metal cation is removed by the hydrogen type strong acid cation exchange resin. The low salt water is reused by the reverse osmosis system, and the high salt water is removed by the chelating type ion exchange resin. The high salt water is evaporated and concentrated to the solid after pH adjustment and flocculation treatment to become harmless solid impurities. The condensate is recycled for use, Or the high salt water is treated by chelating ion exchange resin, and then discharged directly after the COD reaches the standard through ultraviolet photocatalytic oxidation;