Electroplating equipment manufacturer The control of the production process temperature is the top priority in the electroplating process. If the temperature fluctuates greatly, it will immediately damage the electroplating quality, and will also cause extravagance and waste of power energy. Current Electroplating equipment At the time of the design concept, we had fully considered this point, and set the pre heating effect on its industrial touch screen, according to which we can set the pre heating time. At the same time, the heating system of electroplating equipment also includes service facilities such as level gauge control equipment, automatic moisturizing and water replenishing equipment, which can maintain the effect of automatic level gauge compensation when the level gauge is lower than the set level gauge. So as to maintain the system and prevent the heating pipe from air burning or safety accidents. On the other hand, PID fuzzy control is used to avoid adverse effects caused by temperature.
What is the purpose of the application of electroplating equipment for electronic components? The use of all mechanical equipment often has a relative purpose that must be maintained, which is all due to the actual application of mechanical equipment. For example, electroplating equipment for electronic components can be used in the production and processing of electronic products only when it is convenient to maintain the following purposes.
First, improve the security features of electronic products: based on the use of electronic component electroplating equipment in the production and processing of electronic products, it can be thought of as an electrodeposit on the surface of electronic products. With this electrodeposit, it can improve the wear resistance and corrosion resistance of iron castings, It can promote the application of electroplated electronic products against the adverse effects of various external factors. From this point of view, it is usually necessary to use this kind of mechanical equipment in the production and processing of electronic components, which is convenient to maintain and improve the security features of electronic products. Secondly, improve the architectural art of electronic products: by applying electronic component electroplating equipment to the production and processing of electronic products, electroplating equipment manufacturers can improve the unique style of electronic products based on the desired coating on the surface of electronic products, so as to improve the architectural art of electronic products. These are all kinds of mechanical equipment, and the application purpose that must be maintained in the application is the first.
Not all positive ions of metal composites can be deposited from the aqueous solution. If the side effect of the reduction of hydroxyl ions to hydrogen on the negative electrode is important, the positive ions of metal composites cannot be melted on the negative electrode. According to the experiment, the probability of positive ions of metal composites electrodepositing from the aqueous solution can be obtained from the periodic table of elements, See the legend in Table 1.1.
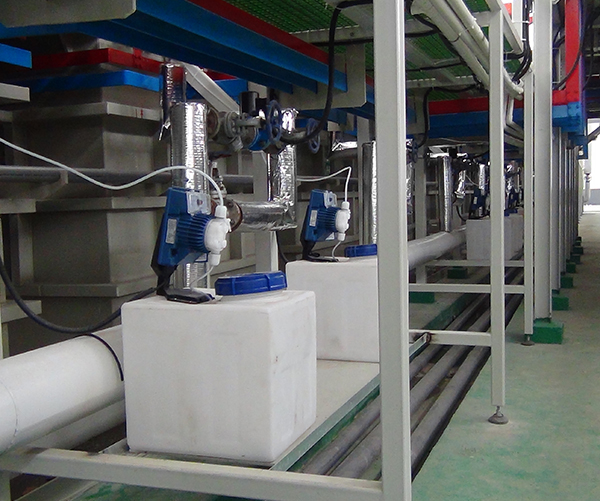
Anodic treatment can be divided into soluble anodic treatment and insoluble anodic treatment. The vast majority of anodic treatment is soluble anodic treatment corresponding to the coating, for example, hot-dip galvanizing is zinc anode, electroplated nickel/nickel/silver is silver anode treatment, and electroplated tin violet lead alloy is treated with tin lead alloy anode. However, very few electroplating uses insoluble anode treatment due to the difficult dissolution of anodic treatment, For example, platinum or titanium anodes are commonly used for pH hot stamping. The positive ion of the main salt of the plating solution is compensated by adding a standard gold containing solution. The stainless steel plate is anodized with pure lead, lead tin aluminum alloy profiles, lead antimony aluminum alloy profiles and other insoluble anodes.
Thyristor switching power supply Thyristor switching power supply shall use light electronic circuit to adjust the working frequency, very light, high efficiency, convenient and fast supervision, reliable quality and not easy to damage. The difference between the thyristor and the general silicon rectifier tube is that the thyristor has a control pole, which controls the thyristor conduction time according to the operating frequency of the control pole, and then controls the output operating frequency. There are two important methods for thyristor electroplating power supply in power circuit structure:
1. Thyristor shall be used for voltage transformation on several sides of power frequency transformer, and then silicon tube polyphase ballast shall be used on the secondary side.
2. Immediately use the thyristor to conduct the transformer ballast at the secondary side of the power frequency transformer.
At present, most of the rectifier transformers are three-phase electric five column core energy-saving transformers, which eliminates the balance reactor, reduces the direct cost and improves the efficiency compared with the ballast mode of six phase double reverse active balance reactor. The maintenance of silicon controlled power supply is more complicated. During the maintenance, the mechanical fault position shall be distinguished first. At the beginning, the AC current of the digital multimeter shall be 2.5V, the control pole shall be disconnected, and the operating frequency of the thyristor control pole shall be measured. Adjust the control knob. If the operating frequency is about 0~IV (different thyristors, different operating frequency values), open the control part and everything is normal, and the thyristors are abnormal. If there is no operating frequency or the operating frequency value is not large, it is found that the control board is abnormal. First, check whether the working voltage and synchronous working frequency input by the control board are normal. After eliminating the mechanical fault of the transformer with the working voltage and synchronous working frequency provided, the mechanical fault will be concentrated on the open board, which needs to be disassembled or sent for repair.