If some reason is encountered. Some maintenance work needs to be done, Electroplating equipment It takes a long time without words. To avoid shortening the service life of electroplating equipment due to idleness
The main work is to make sure that there is no water or dust, and clean the workshop. Electroplating automatic production line, to ensure that the workshop environment is clean and dry; All motors shall be wrapped with fresh paper for protection; All bearings are injected with lubricating grease to prevent rust. All rubber wheel bearings on the crane shall be filled with lubricating grease for rust prevention; In order to prevent aging, all the parts sprayed with rhizopus shall be wrapped with fresh paper to protect the crane lifting sling.
The liquid medicine in all pipelines shall be completely discharged; The medicine water in the persimmon filtered by the filter is clean; Take out the filter element and clean it; The solenoid valve, pressure valve and flowmeter on the pipeline shall be wrapped with fresh paper; Take out and clean all heaters in the tank; More than 80% of electroplating failure rate occurs in the pre-treatment process, so the pre-treatment effect is particularly important. The appearance of the substrate affects the coating structure and adhesion. The pretreatment of plated parts is one of the most important factors that determine the quality of electroplating.
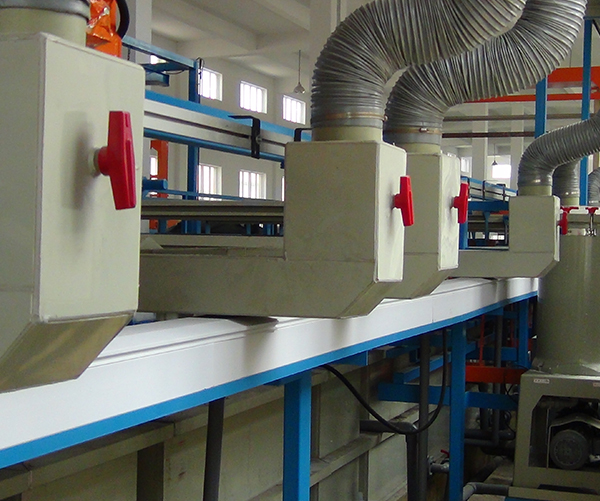
In actual production. The influence of the surface state of the substrate on the structure of the coating the size, shape and arrangement of crystals or crystals determine the structural characteristics of the coating. In the automatic electroplating production line, the structural characteristics of metal coatings in different electroplating solutions are also different, mainly due to different stacking processes. At the beginning of electroplating, the surface of the base material first generates some tiny spots, namely crystal cores. As time goes on, the number of single crystals increases, and they are connected to each other to form a coating.